Professional Investment Casting Service for Custom Parts In China
• Over 20 Years Experience • Quick Response • Top Quality at Low Cost
Certifications: ISO 9001:2015





35000+
Parts fabricated each month
46000+
Product developers served
1000+
Parts within days
Free Design for Manufacturability Analysis
Tracking the Whole Range of Project with Weekly Report for Customers
Production Cost-down Evaluation
The Ability to Offer MOQ of as Little as 100.
Over 20 Years Experience
Investment Casting Materials
Material | Grade | Material | Grade |
Aluminum | A356/A380/B206 | Stainless Steel | SS303/SS304/SS316/SS316L |
Steel | A395/A679/A48/A536 | Brass | C83600/C84400/C95800 |
The Tolerances We Can Achieve
With Drawing | Without Drawing | |
Linear Dimension | +/-0.1mmISO 2768-mk | ISO 2768 Course |
Hole | +/-0.05 mmISO 2768-mk | ISO 2768 Course |
Angular | +/- 0.1 degree | ISO 2768 Course |
Surface Finishing Options
Name | Applicable Materials | Colors | Can Be Applied with |
Anodizing | Aluminum | Clear, black, grey, red,blue, gold | Media Blasting, Tumbling, Alodine |
Electroless Nickel Plating | Aluminum, Steel,Stainless Steel | - | Media Blasting, Tumbling |
Media Blasting | Aluminum, Steel,Stainless Steel, Brass,Bronze, Copper | - | All post processes except Electro polish and Powder coat |
Nickel Plating | Aluminum, Steel,Stainless Steel | - | Media Blasting, Tumbling |
Powder Coating | Aluminum, Steel,Stainless Steel | Pantone or RAL colormatching | - |
Tumbling | Aluminum, Steel,Stainless Steel, Brass, Bronze, Copper | - | All post processes except Electro polish and Powder coat |
Investment Casting Products Display
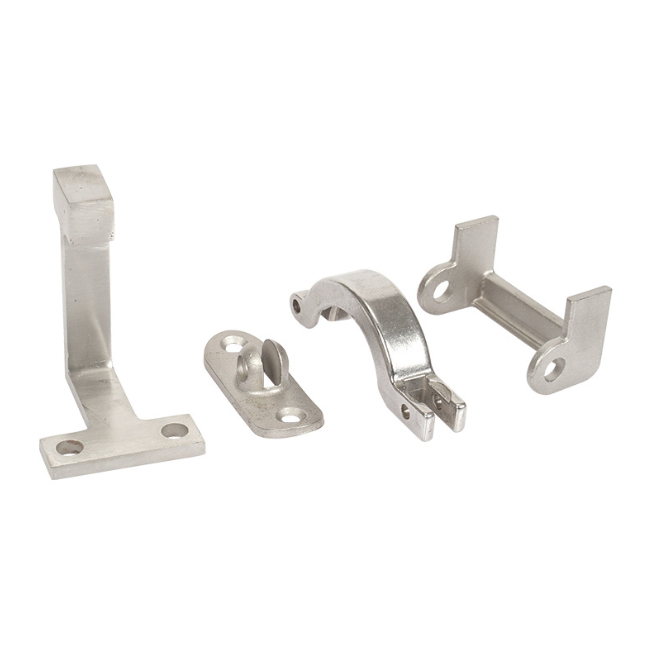
Material: SS304
Size: N/A
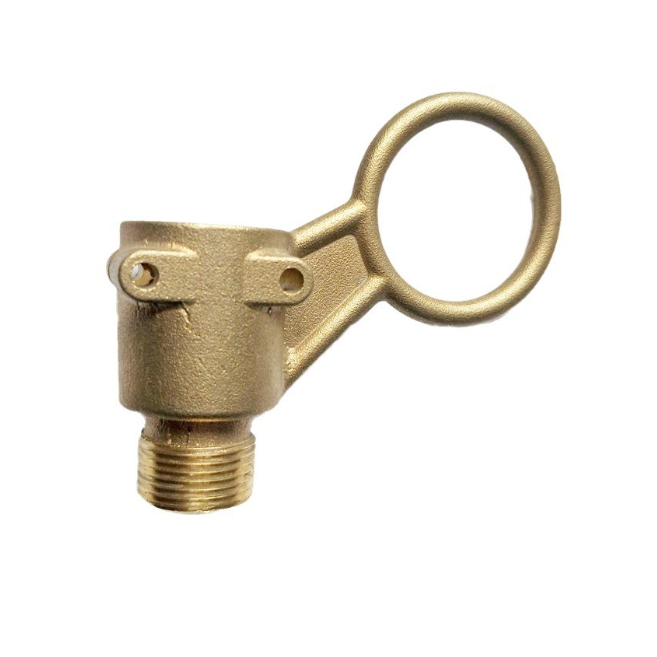
Material: Brass
Size:200 X 150 X 50MM
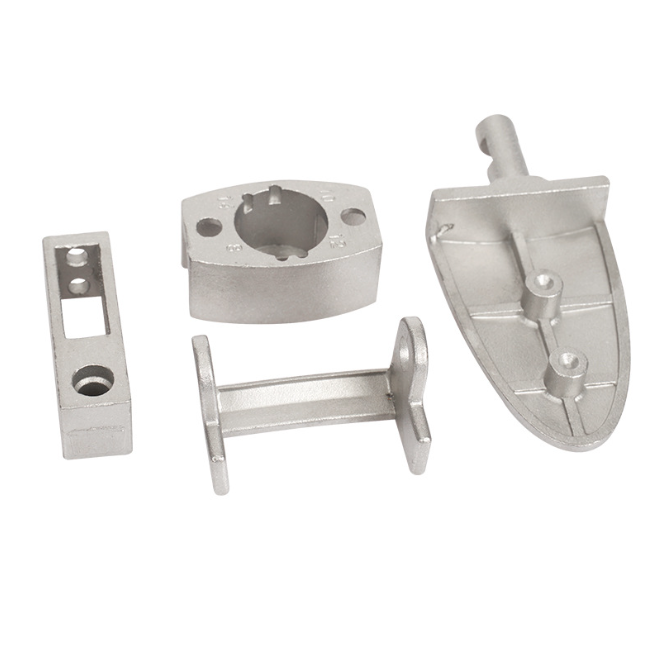
Material: SS316
Size: N/A
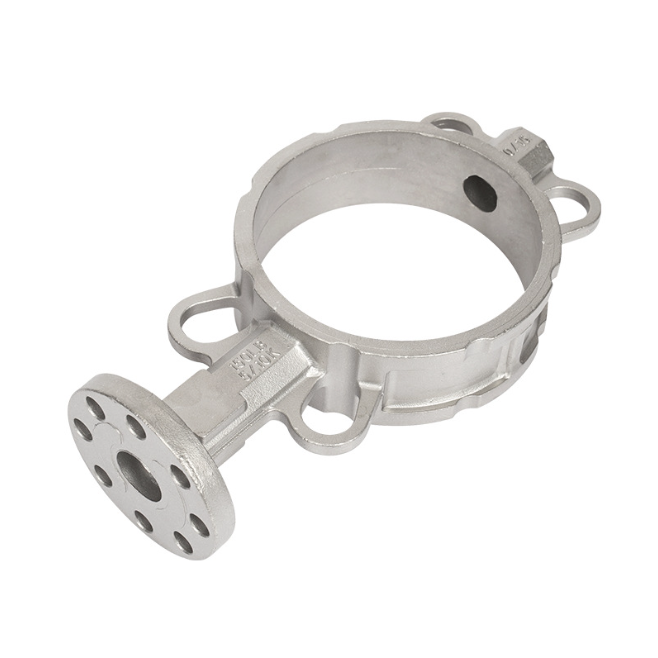
Material: Carbon Steel
Size: 220 X 120 X 30MM
Investment Casting in Manufacturing Group
Manufacturing Group is a professional casting services company, we are your partner in casting manufacturing. With more than 20 years of experience in the industry. Our creative team of engineers takes care of every detail to make sure you get the highest quality parts at low cost.
It all starts with filling out our Request for Quote Form. You’ll receive your quote quickly, allowing you to make the most of your time.
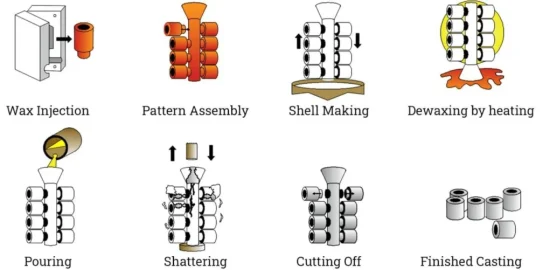
Why Choose US?
Compared with the competitors in China, we are able to provide the following advantages:
- Very competitive prices. We keep your projects on time and on budget.
- High quality, extremely low cost tooling.
- Reliable product quality overseen by our own engineering and quality personnel.
- The ability to offer minimum order quantities of as little as 100.
- Design and prototyping capabilities.
- We strive to exceed your expectations.
You can enjoy the following benefits in cooperation with us:
- Secured payment (We will take full responsibilities for the compensation resulting from any product faults)
- Product of high quality with the most competitive price.
- Quick response (We will reply to your questions and requests with 12 hours)
- Tracking the whole range of project at your home (a weekly progressive report will be prepared for our customers)
- Prompt delivery.
Just tell us what you need and we are right here to serve your requests and get your goods transported to your company in time. It’s very easy for you.
So, why not contact us right away to check out by yourself?
Don't know What To start with?
Start precision manufacturing with our services -making every product perfect
Learn More About Investment Casting Services
Investment casting is a manufacturing process used to create metal parts with intricate shapes and high precision. Here’s a brief overview of how it works:
Pattern Creation: A pattern of the desired object is made, often from wax or a thermoplastic material. This pattern is an exact replica of the final part.
Shell Building: The pattern is coated with a ceramic material to create a shell. This is typically done by dipping the pattern into a slurry and then allowing it to dry. Multiple layers may be applied to achieve the right thickness.
Pattern Removal: The coated shell is then heated to melt and remove the wax or plastic pattern, leaving a hollow ceramic shell. This is often referred to as “lost-wax casting.”
Metal Pouring: Molten metal is poured into the empty shell, filling the cavity that was once occupied by the pattern.
Cooling and Shell Removal: After the metal cools and solidifies, the ceramic shell is broken away, revealing the cast metal part.
Investment casting is valued for producing complex shapes with excellent surface finishes and tight tolerances, making it widely used in industries like aerospace, automotive, and medical manufacturing.
Investment casting can be categorized into several types based on different criteria such as the pattern material, the shell material, the type of metal used, and the casting process itself. Here are some common types:
Lost-Wax Casting: This is the most traditional form of investment casting, where the pattern is made from wax. After waxing, a shell is created, which is then heated to remove the wax.
Lost-Foam Casting: Instead of using a solid pattern, this method uses a foam pattern that is vaporized when molten metal is poured into the cavity. This allows for complex shapes and reduces the need for shell building.
Ceramic Shell Casting: In this method, the shell is built up using a ceramic material instead of the traditional sand or plaster. It allows for finer details and smoother finishes.
Cold Chamber vs. Hot Chamber: Depending on the type of metal being poured:
- Cold Chamber: Used for metals with high melting points, where molten metal is poured into the mold from a separate chamber.
- Hot Chamber: Typically used for lower melting point metals, where the chamber is submerged in the metal.
Aluminum Investment Casting: Specifically for aluminum parts, this process utilizes a specific setup tailored to the properties of aluminum.
Stainless Steel Investment Casting: This is specialized for casting stainless steel parts, commonly used in aerospace and medical applications.
Precision Investment Casting: Refers to investment casting with tight tolerances and excellent surface finishes for high-performance applications.
Each type of investment casting has its own advantages and is chosen based on the specific requirements of the final part, including material properties, complexity, and production volume.
Investment casting, while offering many benefits, also has some limitations. Here’s a concise overview of the advantages and disadvantages of this manufacturing process:
Advantages
High Precision: Investment casting produces parts with excellent dimensional accuracy and surface finish, reducing the need for extensive machining.
Complex Geometries: It can create intricate shapes and designs that are difficult or impossible to achieve with other casting methods.
Material Versatility: A wide range of metals, including alloys, can be used, allowing for tailored properties based on the application.
Minimal Waste: The process generates less scrap material compared to some other methods, making it more efficient.
Consistency: It can produce large quantities of identical parts with consistent quality, ideal for mass production.
Reduced Assembly: Complex parts can be made in a single piece, eliminating the need for multiple components and assembly.
Disadvantages
Higher Costs: The initial costs for patterns and setup can be high, making it less economical for small production runs.
Longer Lead Times: The process can be time-consuming, especially for the shell-building phase and cooling, which might delay production.
Limited to Certain Materials: While versatile, some materials, particularly those with very high melting points, may not be suitable for investment casting.
Brittleness: Parts made from certain alloys can be brittle, especially if not designed properly, leading to potential failure in service.
Complex Process: The multi-step nature of investment casting requires skilled labor and precise control over each step, increasing the likelihood of errors.
Environmental Concerns: The production of ceramic shells and some materials used in the process can have environmental implications if not managed properly.
Balancing these advantages and disadvantages helps manufacturers determine if investment casting is the right choice for their specific needs.
The tolerance of investment casting can vary based on several factors, including the complexity of the part, the material used, and the specific requirements of the manufacturing process. Generally, investment casting is known for its capability to achieve tight tolerances. Here are some typical tolerance ranges you can expect:
General Tolerance Ranges
Dimensional Tolerances:
- Standard tolerances for investment casting can range from ±0.005 inches (±0.127 mm) for smaller parts to ±0.015 inches (±0.381 mm) for larger and more complex geometries.
- For very intricate designs, tolerances can be tighter, sometimes achieving ±0.001 inches (±0.025 mm).
Geometric Tolerances:
- Investment casting can also maintain good geometric tolerances, such as flatness, parallelism, and perpendicularity, often within 0.005 inches (0.127 mm) to 0.010 inches (0.254 mm).
Surface Finish:
- The surface roughness of investment cast parts can typically range from Ra 125 to Ra 250 (roughness average in microinches), with potential for even finer finishes depending on the subsequent machining or polishing processes.
Factors Influencing Tolerances
- Design Complexity: More intricate designs may require adjustments to the anticipated tolerances.
- Material Properties: Different metals and alloys behave differently during solidification and cooling, which can affect dimensional stability.
- Shell Thickness: Thicker shells may introduce more variability in dimensions.
- Process Control: The precision of the equipment and the skill of the operators can also influence the tolerances achievable.
Conclusion
Overall, investment casting is capable of achieving superior tolerances compared to many other casting methods, making it suitable for high-precision applications in industries like aerospace, automotive, and medical devices.