Professional Gravity Casting Service for Custom Parts
• Over 20 Years Experience • Quick Response • Top Quality at Low Cost
Certifications: ISO 9001:2015





35000+
Parts fabricated each month
46000+
Product developers served
1000+
Parts within days
Free Design for Manufacturability Analysis
Tracking the Whole Range of Project with Weekly Report for Customers
Production Cost-down Evaluation
The Ability to Offer MOQ of as Little as 100.
Over 20 Years Experience
Gravity Casting Materials
Material | Grade | Material | Grade |
Aluminum | A356/A380/B206 | Stainless Steel | SS303/SS304/SS316/SS316L |
Steel | A395/A679/A48/A536 | Brass | C83600/C84400/C95800 |
The Tolerances We Can Achieve
With Drawing | Without Drawing | |
Linear Dimension | +/-0.1mmISO 2768-mk | ISO 2768 Course |
Hole | +/-0.05 mmISO 2768-mk | ISO 2768 Course |
Angular | +/- 0.1 degree | ISO 2768 Course |
Surface Finishing Options
Name | Applicable Materials | Colors | Can Be Applied with |
Anodizing | Aluminum | Clear, black, grey, red,blue, gold | Media Blasting, Tumbling, Alodine |
Electroless Nickel Plating | Aluminum, Steel,Stainless Steel | - | Media Blasting, Tumbling |
Media Blasting | Aluminum, Steel,Stainless Steel, Brass,Bronze, Copper | - | All post processes except Electro polish and Powder coat |
Nickel Plating | Aluminum, Steel,Stainless Steel | - | Media Blasting, Tumbling |
Powder Coating | Aluminum, Steel,Stainless Steel | Pantone or RAL colormatching | - |
Tumbling | Aluminum, Steel,Stainless Steel, Brass, Bronze, Copper | - | All post processes except Electro polish and Powder coat |
Gravity Casting Products Display
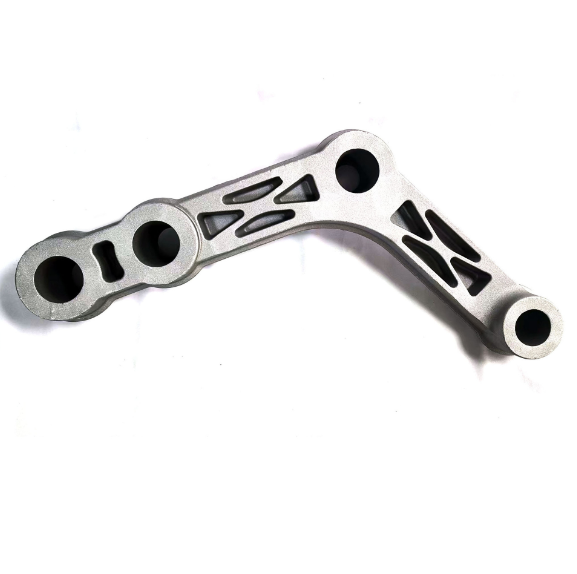
Material: Aluminium
Size:400 X 100 X 30MM
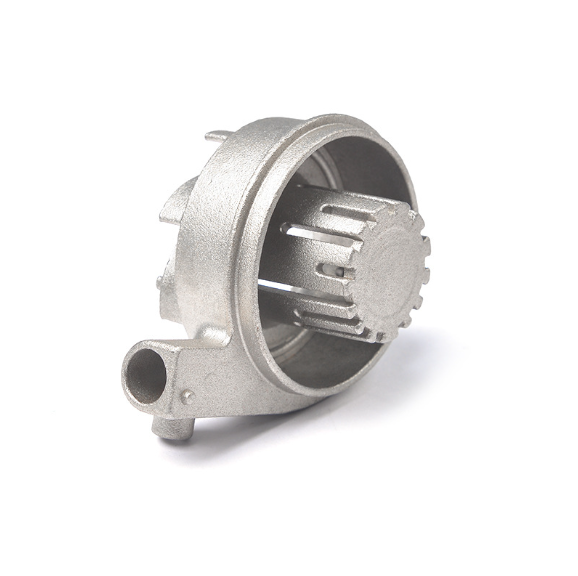
Material: Aluminium
Size:200 X 240 X 50MM
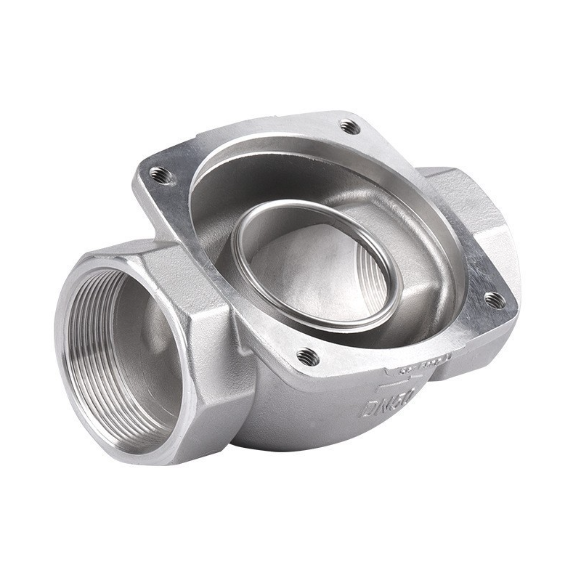
Material: SS304
Size:200 X 160 X70MM
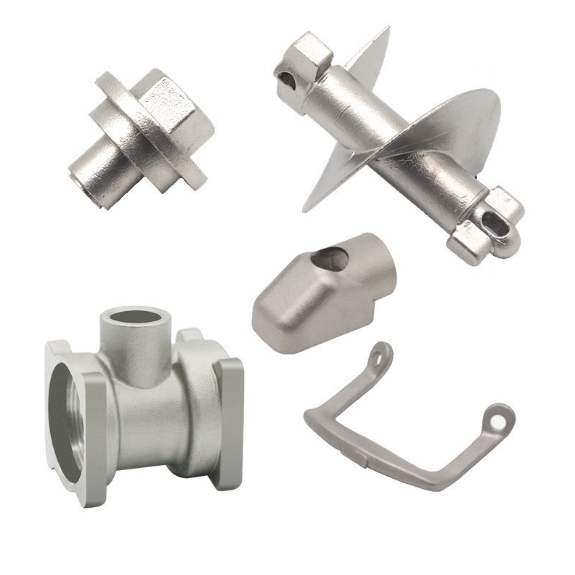
Material: Carbon Steel
Size: N/A
Gravity Casting Services in Manufacturing Group
Manufacturing Group – Casting Engineering is a professional casting services company, we are your partner in casting manufacturing. With more than 20 years of experience in the industry. Our creative team of engineers takes care of every detail to make sure you get the highest quality parts at low cost.
It all starts with filling out our Request for Quote Form. You’ll receive your quote quickly, allowing you to make the most of your time.
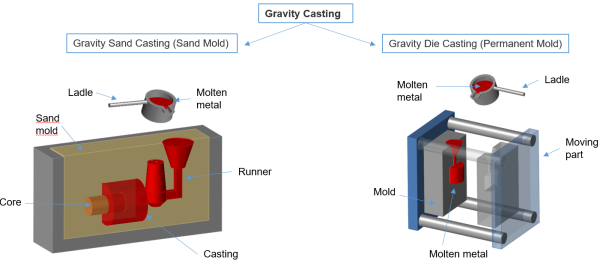
Why Choose US?
Compared with the competitors in China, we are able to provide the following advantages:
- Very competitive prices. We keep your projects on time and on budget.
- High quality, extremely low cost tooling.
- Reliable product quality overseen by our own engineering and quality personnel.
- The ability to offer minimum order quantities of as little as 100.
- Design and prototyping capabilities.
- We strive to exceed your expectations.
You can enjoy the following benefits in cooperation with us:
- Secured payment (We will take full responsibilities for the compensation resulting from any product faults)
- Product of high quality with the most competitive price.
- Quick response (We will reply to your questions and requests with 12 hours)
- Tracking the whole range of project at your home (a weekly progressive report will be prepared for our customers)
- Prompt delivery.
Just tell us what you need and we are right here to serve your requests and get your goods transported to your company in time. It’s very easy for you.
So, why not contact us right away to check out by yourself?
Don't know What To start with?
Start precision manufacturing with our services -making every product perfect
Learn More About Gravity Casting Services
Gravity casting is a manufacturing process used to produce metal parts by pouring molten metal into a reusable mold, known as a die. Here’s how it works:
Mold Creation: The die, typically made from steel or iron, consists of two halves that are precisely machined to form the desired shape of the part. The die is designed to withstand high temperatures and pressures.
Melting Metal: The metal, usually aluminum, zinc, or magnesium, is melted in a furnace until it reaches a liquid state.
Pouring: The molten metal is poured into the die under the influence of gravity, hence the name “gravity die casting.” Unlike pressure die casting, which uses a mechanical pump to force the metal into the mold, gravity casting relies on gravity alone to fill the mold.
Solidification: The molten metal fills the cavity of the die and begins to cool and solidify. This process can take several seconds to a few minutes, depending on the thickness and material.
Ejection: Once the metal has solidified, the die is opened, and the finished part is ejected.
Advantages of Gravity Casting:
- Cost-Effective: It typically has lower tooling costs compared to high-pressure die casting, making it suitable for lower-volume production.
- Good Surface Finish: It often yields parts with a high-quality surface finish and good dimensional accuracy.
- Material Versatility: This method can be used with a variety of metals, typically lighter alloys.
Applications:
Gravity casting is widely used in industries such as automotive, aerospace, and consumer goods to produce components like engine blocks, housings, and various fittings.
If you need further details on specific aspects of gravity die casting, feel free to contact us!
Gravity casting can be categorized into two main types, each characterized by the way molten metal is poured and the type of dies used. Here are the primary types:
Open-Top Gravity Casting:
- Description: In this method, the molds are designed without a top section, allowing the molten metal to flow in from above. This method is simpler and allows for easier access when pouring the metal.
- Advantages: Easier to handle large and complex parts, and less prone to entrapment of gases since there is a direct flow of metal.
- Applications: Commonly used for larger components, such as certain automotive parts or machine housings.
Closed-Die (or Semi-Closed Die) Gravity Casting:
- Description: This method uses molds that seal completely on the sides, with a pouring hole at the top (or occasionally at the side). The closed design can help control the flow of the molten metal and reduce oxidation.
- Advantages: Better for creating precise shapes and details, providing superior dimensional accuracy, and often offering better mechanical properties due to controlled cooling.
- Applications: Suitable for smaller, more intricate components found in electronics, aerospace, and automotive industries.
Other Considerations:
- Permanent Molds: Both open-top and closed-die methods utilize permanent molds made of steel or iron, which can withstand multiple cycles of casting.
- Variations in Process: The specific techniques and equipment may vary within these categories, including automated pouring systems or manual methods, depending on production scale and part requirements.
Advantages of Gravity Casting:
Cost-Effective for Low to Medium Volume Production:
- Lower tooling costs compared to high-pressure die casting make it ideal for smaller production runs or prototypes.
Good Surface Finish:
- Parts produced by this method often have a smooth surface finish, reducing the need for extensive post-processing.
Dimensional Accuracy:
- High precision and repeatability can be achieved, resulting in parts that closely match the intended design specifications.
Less Porosity:
- The process can produce denser parts with minimal gas entrapment, which is beneficial for mechanical properties.
Versatile with Materials:
- A wide range of metals and alloys can be used, such as aluminum, zinc, magnesium, and certain copper alloys.
Reusability of Molds:
- The use of durable steel molds allows for repeated casting, which can significantly lower per-part costs over time.
Complex Geometries:
- Capable of producing complex shapes, offering design flexibility in the manufacturing process.
Disadvantages of Gravity Casting:
Limited to Certain Shapes and Sizes:
- Not suitable for extremely complex geometries or very large components that require high precision.
Longer Cycle Times:
- The cooling and solidification times can be longer than in other methods like high-pressure die casting, potentially affecting production speed.
Initial Tooling Costs:
- While cheaper than high-pressure die casting for small runs, the initial investment in steel molds can be significant.
Requires Skilled Labor:
- Handling molten metals and operating die casting machines safely requires skilled operators to minimize risks.
Less Suitable for High-Volume Production:
- For very high-volume applications, high-pressure die casting may be more efficient and economical.
Risk of Dimensional Variation:
- Variations in cooling rates or pouring techniques can lead to dimensional variations in the final product.
Surface Defects:
- While surface finishes are generally good, defects such as dross or surface imperfections can still occur if not managed properly.
Conclusion:
Gravity casting is an effective method for many applications, especially when balancing quality, cost, and production volume. However, it may not be the best choice for all scenarios, particularly those requiring tight tolerances or extreme precision at high volumes.
The tolerances of gravity casting can vary depending on several factors, such as the complexity of the part, the design of the mold, the material being cast, and the specific requirements of the application. However, precision in gravity casting typically allows for the following general tolerances:
Typical Tolerances:
General Tolerances:
- For most gravity die cast parts, tolerances can range from ±0.5 mm to ±1.5 mm for dimensions up to 100 mm.
- For larger parts (dimensions over 100 mm), tolerances might be in the range of ±1.0 mm to ±3.0 mm.
Precision Tolerances:
- With careful design and machining of the die, tighter tolerances (about ±0.3 mm) may be achievable, especially for smaller, intricately shaped components.
Geometric Tolerances:
- Geometric tolerances (like flatness, roundness, etc.) can also be specified. These are often within 0.1 mm to 0.5 mm depending on the complexity of the part.
Factors Affecting Tolerances:
- Material Properties: Different metals and alloys may behave differently during the casting process, affecting dimensional stability.
- Cooling Rates: Variations in cooling can lead to changes in dimensions due to thermal contraction.
- Design Complexity: More complex designs may result in greater deviations from nominal dimensions, necessitating tighter control in mold design.
- Machining Processes: Post-casting machining can improve accuracy but can add to production costs and time.
Best Practices:
- Working closely with engineers during the design phase can help optimize tolerances for manufacturing efficiency and part performance.
- Utilizing advanced CAD software and simulation tools can also help in predicting outcomes and refining tolerances.