Professional Die Casting Service for Custom Parts in China
• Over 20 Years Experience • Quick Response • Top Quality at Low Cost
Certifications: ISO 9001:2015





50000+
Parts fabricated each month
48000+
Product developers served
1500+
Parts within days
Free Design for Manufacturability Analysis
Tracking the Whole Range of Project with Weekly Report for Customers
Production Cost-down Evaluation
The Ability to Offer MOQ of as Little as 100.
Over 20 Years Experience
Die Casting Materials
We provide a variety of materials for creating die casting parts, but please keep in mind that we can provide different materials upon request. If you want to check more materials, please contact us.
Material | Grade | Properties |
Aluminium |
|
|
Zinc |
|
|
Magnesium |
|
|
The Tolerances We Can Achieve
With Drawing | Without Drawing | |
Linear Dimension | +/-0.1 mm +/-0.004 inch ISO 2768-mk | ISO 2768 Course |
Angular | +/- 0.5 degree | ISO 2768 Course |
Tolerances listed here are minimums for an ideal case. Looser tolerances may be needed based on process, material, or part design.
Surface Finish Options
Name | Applicable Materials | Colors | Can Be Applied with |
Anodizing | Aluminum | Clear, black, grey, red,blue, gold | Media Blasting, Tumbling, Alodine |
Electroless Nickel Plating | Aluminum, Steel,Stainless Steel | - | Media Blasting, Tumbling |
Media Blasting | Aluminum, Steel,Stainless Steel, Brass,Bronze, Copper | - | All post processes except Electro polish and Powder coat |
Nickel Plating | Aluminum, Steel,Stainless Steel | - | Media Blasting, Tumbling |
Powder Coating | Aluminum, Steel,Stainless Steel | Pantone or RAL colormatching | - |
Tumbling | Aluminum, Steel,Stainless Steel, Brass, Bronze, Copper | - | All post processes except Electro polish and Powder coat |
Die Casting in Manufacturing Group
Manufacturing Group is a professional die-casting services company, we are your partner in die-casting manufacturing. With more than 20 years of experience in the industry. Our creative team of engineers takes care of every detail to make sure you get the highest quality parts at low cost.
It all starts with filling out our Request for Quote Form. You’ll receive your quotation quickly, allowing you to make the most of your time.
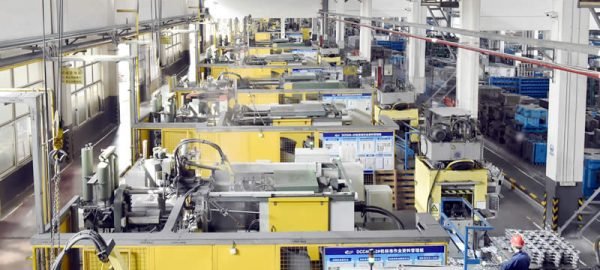
Why Choose US?
Compared with the competitors in China, we are able to provide the following advantages:
- Very competitive prices. We keep your projects on time and on budget.
- High quality, extremely low cost tooling.
- Reliable product quality overseen by our own engineering and quality personnel.
- The ability to offer minimum order quantities of as little as 100.
- Design and prototyping capabilities.
- ISO 9001:2015 quality accreditation.
- We strive to exceed your expectations.
You can enjoy the following benefits in cooperation with us:
- Secured payment (We will take full responsibilities for the compensation resulting from any product faults)
- Product of high quality with the most competitive price.
- Quick response (We will reply to your questions and requests with 12 hours)
- Tracking the whole range of project at your home (a weekly progressive report will be prepared for our customers)
- Prompt delivery.
Just tell us what you need and we are right here to serve your requests and get your goods transported to your company in time. It’s very easy for you.
So, why not contact us right away to check out by yourself?
Don't know What To start with?
Start precision manufacturing with our services -making every product perfect
Learn More About Die-Casting Services
Die-casting services involve a manufacturing process where molten metal is injected into a mold (die) to create precise and complex metal parts. This process is typically used for producing high volumes of metal components with excellent dimensional accuracy and surface finish.
Here’s a brief overview of how it works:
Mold Creation: A die (mold) is designed and manufactured, usually from hardened steel for durability. The mold is made to the exact specifications of the part to be produced.
Metal Injection: Molten metal—commonly aluminum, zinc, or magnesium—is injected under high pressure into the cavity of the mold.
Cooling and Solidification: The molten metal cools and solidifies within the mold, taking on its shape.
Ejection: Once solidified, the mold opens, and the finished part is ejected.
Finishing: After ejection, parts may undergo additional finishing processes, like trimming, machining, or surface treatment, depending on the specifications.
Die-casting is widely used in various industries, including automotive, aerospace, electronics, and consumer goods, due to its ability to produce lightweight, durable, and complex shapes efficiently.
If you need more specific details about the types of die-casting or applications, feel free to contact us!
There are primarily two types of die-casting processes, each suited for different applications and material properties: high-pressure die casting and low-pressure die casting. Here’s a closer look at each type, along with a brief overview of a specialized method called gravity die casting:
1. High-Pressure Die Casting (HPDC)
- Process: Molten metal is injected into a mold at high pressure (up to 30,000 psi). This method allows for the creation of intricate and highly detailed shapes.
- Materials: Commonly used with aluminum, zinc, and magnesium alloys.
- Advantages:
- High dimensional accuracy and good surface finish.
- Suitable for mass production, allowing for fast cycle times.
- Ability to produce thin walls and complex geometries.
2. Low-Pressure Die Casting (LPDC)
- Process: Molten metal is poured into a mold and then allowed to fill the cavity under low pressure (generally around 1 to 15 psi). This method is often used for larger or thicker components.
- Materials: Typically involves aluminum and sometimes zinc alloys.
- Advantages:
- Improved mechanical properties due to slower filling rates.
- Better control over the cooling process.
- Reduced porosity compared to high-pressure methods.
3. Gravity Die Casting
- Process: In this method, molten metal is poured into a stationary mold using gravity. It relies on gravity to fill the mold, rather than using pressure.
- Materials: Can use aluminum, zinc, copper, or other non-ferrous metals.
- Advantages:
- Typically lower costs for molds, as they don’t need to withstand as much pressure.
- Offers good quality for components that don’t require intricate designs or high precision.
Additional Processes
- Permanent Mold Casting: Similar to gravity die casting, but the mold can be reused multiple times and is made of metal for better heat retention.
- Thermal Die Casting: This technique involves preheating the mold, allowing specific properties in the final product based on the temperatures used during casting.
Each type of die-casting has its unique advantages and is chosen based on the specific requirements of the part being produced, such as material properties, production volume, and complexity.
Advantages of Die Casting
High Precision and Dimensional Accuracy: Die casting produces parts with tight tolerances, which is crucial for applications requiring exact specifications.
Complex Geometries: The process allows for the creation of intricate shapes and structures that are difficult to achieve with other manufacturing techniques.
Fast Production Rates: Once the die is created, the casting cycle time is rapid, enabling high-volume production with minimal downtime.
Material Efficiency: There is minimal material wastage, as excess metal can often be reused in the process.
Lightweight and Thin-Walled Components: Die casting can produce parts with very thin walls, reducing material use and weight, which is particularly beneficial in automotive and aerospace applications.
Strength and Durability: The die casting process results in a fine grain structure of the metal, enhancing the strength and durability of the manufactured parts.
Consistency and Reproducibility: The method allows for uniform results across large production runs, ensuring quality control and consistency in every piece produced.
Excellent Surface Finish: Parts often come out of the mold with a good surface finish, which can reduce the need for extensive secondary machining and finishing processes.
Versatility in Materials: Die casting can accommodate various non-ferrous metals, such as aluminum, zinc, and magnesium, expanding its applicability across different industries.
Cost-Effectiveness for Large Volumes: For large production volumes, die casting becomes increasingly economical compared to other methods, like machining, due to lower labor and material costs per unit.
Disadvantages of Die Casting
High Initial Tooling Costs: The upfront cost of designing and producing the die can be significant, making it less economical for small production runs.
Limited Material Selection: While versatile, die casting primarily works with non-ferrous metals; ferrous metals are generally not suitable for this process.
Size Limitations: There are practical limits on the size of parts that can be efficiently produced using die casting, as larger components can lead to longer cycle times and higher costs.
Complex Die Maintenance: The dies can wear out over time, leading to maintenance and replacement costs, particularly if producing high volumes of parts.
Porosity and Defects: Depending on the process conditions, cast parts may experience porosity or surface defects, which can affect mechanical properties.
Less Ideal for Low-Volume Production: Die casting is most cost-effective for high-volume runs; low-volume production may not justify the significant initial investment in tooling.
Thermal Sensitivity: The process requires careful control of temperature and cooling rates, as improper management can lead to defects in the cast.
Environmental and Safety Considerations: The use of certain metals and the emissions from molten metal can raise environmental concerns and necessitate strict safety measures.
By weighing these advantages and disadvantages, manufacturers can determine if die casting is the right choice for their specific production needs. If you have more questions or need further details on any point, feel free to contact us!
When designing products for die casting, it’s essential to adhere to specific guidelines to ensure optimal production efficiency, quality, and cost-effectiveness. Here are some key design guidelines for die-casted products:
Design Guidelines for Die Casting
Material Selection:
- Choose materials that are suitable for die casting, such as aluminum, zinc, or magnesium alloys.
- Consider the mechanical properties and thermal characteristics of the material when designing.
Wall Thickness:
- Maintain uniform wall thickness to avoid issues such as warping, uneven cooling, or structural weaknesses.
- Recommended wall thickness typically ranges from 1-4 mm, depending on the material and part design.
Draft Angles:
- Incorporate draft angles (usually 1-3 degrees) on vertical surfaces to facilitate the easy ejection of the part from the die.
- The amount of draft needed may vary based on the part geometry and complexity.
Fillets and Radii:
- Use generous fillets and radii to enhance the flow of molten metal and to reduce stress concentration in corners.
- Sharp corners can create weak points and lead to defects.
Avoiding Undercuts:
- Minimize or eliminate undercuts, as they complicate the die design and may require additional machining.
- If undercuts are necessary, consider using collapsible cores or slides in the die design.
Parting Line Considerations:
- Design the parting line in a way that it does not interfere with the function of the part or create additional machining requirements.
- Ideally, the parting line should be placed along natural separation features of the part.
Weight Reduction Features:
- Consider using ribs, gussets, or other features to create strength without adding excessive weight.
- Hollow sections can help reduce weight while maintaining structural integrity.
Surface Finish Requirements:
- Specify surface finish requirements, understanding that die-cast parts can achieve a good finish directly from the die, reducing the need for additional machining or finishing.
Assembly Considerations:
- Design parts that can easily be assembled with minimal additional machining or fasteners.
- Incorporate features like locating pins or self-locating geometries where possible.
Thermal Considerations:
- Analyze thermal properties and cooling rates since these can impact part quality and manufacturing speed.
- Design cooling systems in the die to manage temperatures effectively during production.
Design for Machining:
- If machining is required after die casting, consider ‘machining allowances’ in design to ensure that adequate material is available for finishing processes.
Testing and Prototyping:
- Conduct thorough testing and prototyping before committing to full production to identify and rectify potential issues early.
- Use simulation tools to assess flow patterns and thermal dynamics in the die-casting process.
By following these design guidelines, manufacturers can minimize production challenges, enhance part quality, and improve overall efficiency in the die casting process. If you need more details on any specific point or have other questions, feel free to contact us!