Professional Casting Service for Custom Parts in China
• Over 20 Years Experience • Quick Response • Top Quality at Low Cost
Certifications: ISO 9001:2015





35000+
Parts fabricated each month
46000+
Product developers served
1000+
Parts within days
Free Design for Manufacturability Analysis
Tracking the Whole Range of Project with Weekly Report for Customers
Production Cost-down Evaluation
The Ability to Offer MOQ of as Little as 100.
Over 20 Years Experience
Our Casting Services
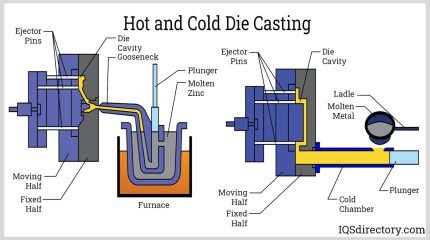
Die Casting Services
Die-casting services refer to a manufacturing process that involves injecting molten metal into a mold to create precise and complex metal parts used in various industries.
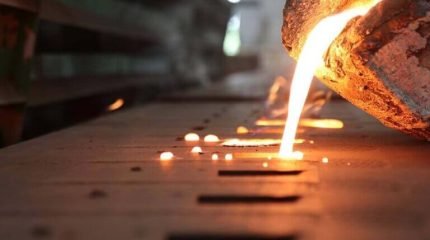
Gravity Casting Services
Gravity casting services involve pouring molten metal into a mold under the force of gravity, allowing it to fill the mold and solidify to create detailed and high-quality metal components.
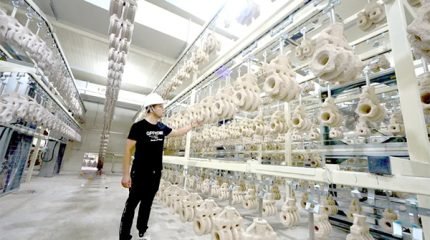
Investment Casting Services
Investment casting services use a wax pattern coated with a ceramic shell; the wax is melted out, leaving a mold for pouring molten metal, creating precise components.
Casting Materials
We provide a variety of materials for creating casting parts, if you want to check more materials, please contact us.
Material | Grade | Properties |
Aluminium |
|
|
Zinc |
|
|
Magnesium |
|
|
Steel |
|
|
Brass | C836000/C84400/C95800 | High machinability, corrosion-resistant, ductile, excellent conductivity, strong, aesthetically pleasing, versatile, weldable. |
Surface Finishing Options
Name | Applicable Materials | Colors | Can Be Applied with |
Anodizing | Aluminum | Clear, black, grey, red,blue, gold | Media Blasting, Tumbling, Alodine |
Electroless Nickel Plating | Aluminum, Steel,Stainless Steel | - | Media Blasting, Tumbling |
Media Blasting | Aluminum, Steel,Stainless Steel, Brass,Bronze, Copper | - | All post processes except Electro polish and Powder coat |
Nickel Plating | Aluminum, Steel,Stainless Steel | - | Media Blasting, Tumbling |
Powder Coating | Aluminum, Steel,Stainless Steel | Pantone or RAL colormatching | - |
Tumbling | Aluminum, Steel,Stainless Steel, Brass, Bronze, Copper | - | All post processes except Electro polish and Powder coat |
Casting Services in Manufacturing Group
Manufacturing Group is a professional casting services company, we are your partner in casting manufacturing. With more than 20 years of experience in the industry.
Our creative team of engineers takes care of every detail to make sure you get the highest quality parts at low cost. It all starts with filling out our Request for Quote Form. You’ll receive your quote quickly, allowing you to make the most of your time.
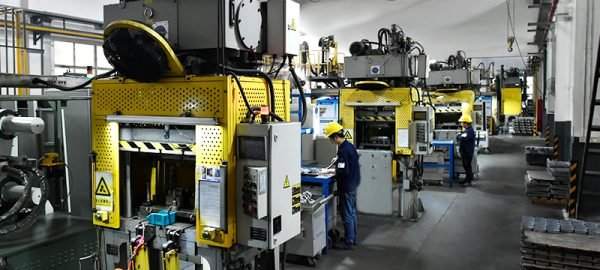
Why Choose US?
Compared with the competitors in China, we are able to provide the following advantages:
- Very competitive prices. We keep your projects on time and on budget.
- High quality, extremely low cost tooling.
- Reliable product quality overseen by our own engineering and quality personnel.
- The ability to offer minimum order quantities of as little as 100.
- Design and prototyping capabilities.
- We strive to exceed your expectations.
You can enjoy the following benefits in cooperation with us:
- Secured payment (We will take full responsibilities for the compensation resulting from any product faults)
- Product of high quality with the most competitive price.
- Quick response (We will reply to your questions and requests with 12 hours)
- Tracking the whole range of project at your home (a weekly progressive report will be prepared for our customers)
- Prompt delivery.
Just tell us what you need and we are right here to serve your requests and get your goods transported to your company in time. It’s very easy for you.
So, why not contact us right away to check out by yourself?
Don't know What To start with?
Start precision manufacturing with our services -making every product perfect
Learn More About Casting Services
Casting is a manufacturing process in which a liquid material, typically metal, is poured into a mold and allowed to solidify form a specific shape. Here’s a breakdown of the process:
Mold Creation: A mold is made, often from materials like sand, metal, or ceramic, to create a cavity in the desired shape of the final product.
Melting: The metal or other material is heated until it reaches a liquid state.
Pouring: The molten material is poured into the prepared mold.
Cooling and Solidifying: The material cools down and solidifies, taking the shape of the mold.
Finishing: After solidification, the mold is removed, and the casting may undergo additional finishing processes such as grinding, polishing, or coating.
Casting is widely used for producing various items, including engine blocks, machine parts, sculptures, and jewelry, due to its ability to create complex shapes and large volumes efficiently. If you need more detailed information or have specific questions, feel free to contact us.
There are several types of casting processes, each suited for different materials, applications, and requirements. Here are some of the most common types:
Sand Casting: A widely used method where a sand-based mold is created, suitable for large and complex parts. It’s cost-effective and can handle a variety of metals.
Investment Casting (or Lost Wax Casting): Involves creating a wax model that is coated in a ceramic shell. Once the shell is formed, the wax is melted away, and liquid metal is poured in. This method is used for precision parts, especially in aerospace and jewelry.
Die Casting: A process primarily used for non-ferrous metals. Metal is injected under high pressure into a steel mold. This method produces parts with excellent dimensional accuracy and surface finish.
Permanent Mold Casting: Involves using a reusable metal mold, which allows for better control of the cooling process. It’s typically used for parts requiring good mechanical properties.
Shell Molding: A variation of sand casting where a thin shell of sand is formed over a pattern, resulting in a high-strength mold that can produce intricate shapes and smooth finishes.
Continuous Casting: A process used primarily in metal production where molten metal is continuously poured into a mold, resulting in a continuous length of material (such as rods or slabs).
Centrifugal Casting: Utilizes centrifugal force to distribute molten metal in a rotating mold. This method is typically used for making pipes and cylindrical parts, allowing for denser and stronger castings.
Lost Foam Casting: Involves creating a mold from foam patterns that vaporize upon pouring molten metal, allowing for complex shapes and reducing the need for core setups.
These casting methods vary in complexity, cost, and application, making them suitable for different manufacturing needs.
Casting is a popular manufacturing process that has its own set of advantages and disadvantages. Here’s a summary:
Advantages of Casting:
Complex Shapes: Casting allows for the production of complex and intricate shapes that may be difficult or impossible to achieve with other manufacturing methods.
Material Versatility: A wide range of materials can be used in casting, including various metals, plastics, and ceramics, making it suitable for diverse applications.
Cost-Effective for Large Volumes: Once the mold is created, casting can be an economical process for mass production, as it allows for the creation of multiple identical parts with minimal additional cost.
Good Surface Finish: Certain casting methods, such as investment casting or shell molding, can produce components with high surface quality, often requiring little or no finishing.
High Strength: Cast parts can provide good mechanical properties, especially when rendered in suitable materials, contributing to the overall strength and durability of the final product.
Reduced Waste: Compared to machining, where material is removed from a larger piece, casting often generates less waste, as it utilizes the material more efficiently.
Disadvantages of Casting:
Initial Costs: The cost of creating molds and patterns can be high, especially for complex designs, making it less economical for small production runs.
Porosity: Castings can have pores or inclusions, which may weaken the final product and affect its mechanical properties.
Dimensional Tolerances: While some casting processes can achieve good tolerances, they are typically not as precise as machining, which may require additional finishing processes.
Surface Defects: Casting processes can lead to defects such as shrinkage, cracks, or rough surfaces, which may necessitate further finishing or reworking.
Limited Material Properties: Some casting techniques can result in anisotropic material properties, meaning that the strength and behavior of the material can vary depending on the direction of the load.
Time-Consuming: The mold-making process can be time-consuming, especially if custom molds are required for each new part design.
Overall, while casting is a versatile and widely used manufacturing process, it is essential to weigh these advantages and disadvantages when deciding if it’s the right method for a specific project. If you need more detailed information or have specific questions, feel free to contact us.
When designing for casting services, several guidelines can help ensure that the end product meets both functional and manufacturability requirements. Here are some important design considerations for casting:
1. Material Selection
- Choose materials compatible with the casting process (e.g., metals, plastics).
- Consider properties such as strength, ductility, corrosion resistance, and thermal stability.
2. Design for Casting Process
- Wall Thickness: Keep wall thickness uniform to prevent shrinkage and warping. Thick sections can lead to longer cooling times and uneven shrinkage.
- Draft Angles: Incorporate draft angles (typically 1-3 degrees) on vertical faces to facilitate easier mold release, especially in sand and die casting.
- Fillets and Rounding: Use fillets (rounded corners) instead of sharp edges to reduce stress concentrations and to improve mold flow and filling.
3. Weight Considerations
- Optimize the design to reduce weight without compromising strength. This can minimize material costs and improve the efficiency of the casting process.
4. Geometric Complexity
- Avoid highly complex geometries that may be difficult to mold or may trap air. If complexity is necessary, consider using core inserts.
5. Draft and Clearance
- Ensure adequate clearance between parts to facilitate assembly and prevent damage during removal from the mold.
- Apply sufficient draft angles to vertical surfaces for easy mold release.
6. Avoiding Undercuts
- Design parts without undercuts as they complicate the mold design and can lead to casting defects. If undercuts are necessary, consider using sliding cores or collapsible cores.
7. Features and Dimensions
- Ribs and Bosses: Incorporate features such as ribs for added structural integrity, but keep them properly designed to avoid mold filling issues.
- Maintain consistent dimension tolerances suitable for casting; typically, tighter tolerances may require additional finishing processes.
8. Casting Allowances
- Include allowances in the design for shrinkage, machining, and other post-processing requirements. This varies with material and process.
9. Surface Finish
- Specify the required surface finish based on functional and aesthetic needs. Some casting methods can achieve smoother finishes than others.
10. Assembly Considerations
- Design cast parts with assembly in mind, including features for joining (such as holes for fasteners) and ensuring accessibility for assembly processes.
11. Testing and Quality
- Consider design elements that facilitate testing and inspection (e.g., suitable locations for measurement and features that indicate quality).
12. Simulation and Prototyping
- Utilize computer-aided design (CAD) tools and simulation software to visualize the casting process and identify potential issues early in the design phase.
13. Environmental Considerations
- Evaluate the environmental impact of the materials and processes used, as well as waste management strategies during casting.
By adhering to these design guidelines, engineers and designers can create parts that are not only functional but also cost-effective and manufacturable through casting processes. If you need more specific details or examples related to a particular casting method or application, feel free to contact us.